About Me
I am a Software Engineer currently working on kinematics algorithms for a surgical robot at Medtronic. I have 6 years of total industry experience. I obtained my Master's degree in Robotics Engineering from WPI(Worcester Polytechnic Institute) and have experience coding in Matlab, simulink, C++, Python, C#, and .Net. ...
Previously, I have worked on QNX applications for robotic controls of catheters, writing communication protocols for a stent placement robotic aide and writing graphical user interfaces for the same. A project very dear to me uses Deep Learning to detect the emotions and attention levels of children with Autism Spectrum Disorder(ASD).
Having a diverse portfolio encompassing Programmable Logic to machine learning has helped me understand systems and subsystems in detail. During my career, I have learned best coding practices in the industry and medical devices in particular.
Moving a lot in my childhood, working in start-ups and medium-sized companies has taught me to adapt quickly and work in any environment. I am a people person and have worked in team sizes ranging from 2 to 25. Some of these were interdisciplinary, ranging from different levels of the organization. It has given me the tools to tackle challenges confidently and made me self-sufficient. I believe I can be an asset anywhere the road takes me.
Medtronic's Robotic Assisted Surgery system is a laparoscopic surgery system that works with teleoperation. I lead(as scrum master) a 6 member kinematics team based fully in India . The team is responsible for New Product development and CAPAs along with improvements. Currently we are working on instrument reliability and Kinematic algorithm optimization.
Software Used: Matlab, Simulink, QNX, C++
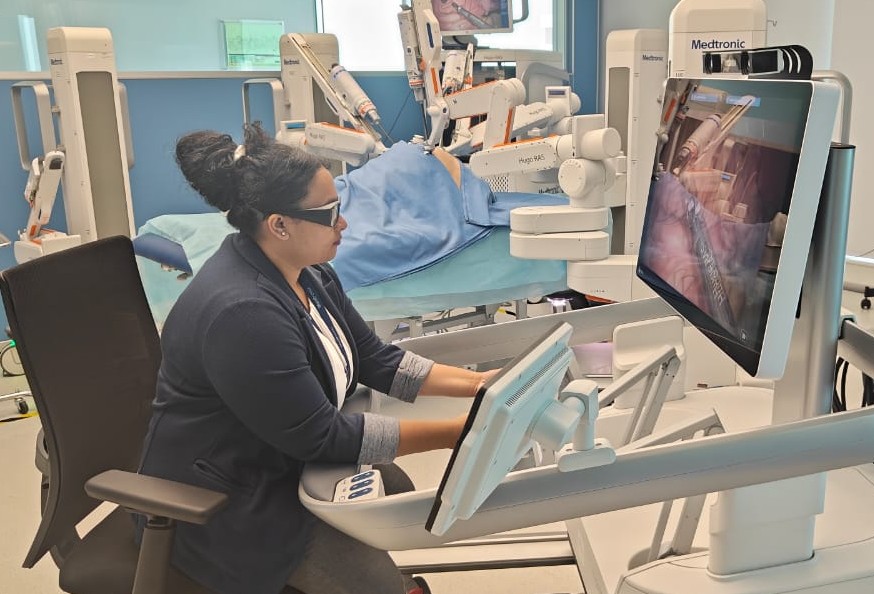
Medacuity is a Software consultancy company and is involved in medical devices specifically. It has several clients in this area and provides software support in the development of these devices.
In my time there I received the Honoring commitments award for delivering what was promised to client under time crunch and working from India add odd hours to make sure the work was complete.
I have worked on medical devices such as catheter and stent placement aiding devices as a UI and robotics developer. As a part of my role, I work on back-end and front-end of devices that operate in a client-server environment. I have also worked on robotic controllers and QNX along with communication protocols for devices and their interfaces. These devices go through rigorous testing as they are medical devices and need FDA approval. It has helped me understand the process and, I have become well versed in the ISO: 13485 that is the software guidelines for medical devices.
Software Used: C++, QNX, QT 15.5.3, Visual studio(C#), python, C, CanBus Communication
Festo is a big name in industrial automation and other pneumatic and hydraulic solutions. Recently they have gotten involved in the liquid handling sector for medical laboratories. It includes valves and pipettes. During development, I supported my team by building test benches and graphical user interfaces for test engineers.
I learned a lot in terms of communication protocols via Ethernet and serial ports. I was involved in the design and testing of products and helped build the firmware for our systems. Most of my job entailed control of PLCs via various interfaces to integrate different components.
Software Used: Codesys, Visual studio(C#), Arduino IDE(C++), Labview, ProCreo, WinIdea(firmware)
During my internship, I designed a test-bed for encoders. The specifications were:
- Minimum number of encoders that can be fit on the test-bed
- Air gap between encoder and encoder ring,
- Foolproof methods of mounting the encoders with the correct air gap
- Easy mounting and removal of encoders to not disturb other encoders
- Cost effectiveness of the test-bed (parts should be standardized and available from manufacturers instead of needing to be machined)
After many iterations, the design was finalized and is displayed below. It has a total of 25 individual components. 11 of them are standard parts that can be bought by the manufacturer and the rest are designed and will have to be manufactured. On repetition of these components, the whole assembly has 221 components.
Software Used: Solidworks
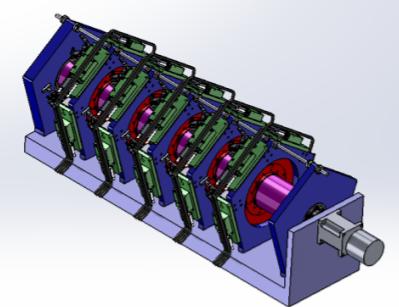
This internship was a great learning opportunity to see how robots interact with each other and humans in an industrial setting. I studied trajectory controllers for 6-DOF Fanuc and ABB robots for car manufacturing. I also learned how to work with Siemens PLCs(Programmable Logic Controllers) and code them using ladder logic. I designed a ladder logic to control a bottle filling station using complex pick and place operations with indexing.
Software Used: SIMANTIC (ladder logic software)
This was research done as a continuation of the project done in my deep learning class. I obtained two other datasets; the CAFE data set and the KDEF data set. These had images of higher resolution but less data than the Kaggle data set. After consideration, we decided to consider their facial features instead of the image as a whole and used the Kaggle data set, CAFE, and KDEF and retrained the network. We also classified the emotions into three categories. Positive, negative, and neutral. Doing this gave a final accuracy of 85.19%
We took inputs from behavioral analysts and used those to train on videos of various children to detect attention level. We used different models to compare the results and validate. These ranged from 80 - 94% accuracy. We used only two classifications of on task and off task.
Since this is part of ongoing research, all the data and results are confidential. I cannot show any videos of the children and how the algorithm worked on the children.
Software Used: Keras, theano, Skitlearn, tensorflow, Python,Harr face detect, feature extraction.
Autism Spectrum Disorder(ASD) is a neurological disorder that causes the late development of motor and social skills. PABI(Penguin for Autism Behavioral Intervention) is a robot that helps children with ASD improve their social skills. It is paired with a tablet and gives various audiovisual queues as positive reinforcement for the right answers.
This project furthers the assistance of the robot by making it capable of recognizing emotions. Doing this can show how much of the sessions are helping the child and keeping them involved.
The FERC Kaggle data set, consisting of 7 emotions (anger, disgust, happy, sad, surprise, fear, and neutral) was used for this project. The dateset had some bad images in it which were removed. It also had an uneven amount of data for each label so, anger and disgust were combined into one as they exhibit a similar negative sentiment. Finally, the data was flipped and augmented to have the same number of samples in each label. It was then put into a pickle file and run on the model. The model consists of various Convolutions, Max-pooling, Flattening, Batch-normalizations, and dropout layers with relu and softmax activation functions.
The maximum accuracy reached on these emotions was 57.22%. On seeing the confusion matrix, it was clear that fear was the weak link. After removing fear, the model trained to an accuracy of 68.50%. The highest accuracy recorded on this data set is 71.2%.
The video below shows how the trained model works on live video test data. I tweaked the final layer to show unsure
if the confidence was less than 50%.
Software Used: Keras, theano, Skitlearn, tensorflow, Anaconda Environment, Python,Harr face detect.
Some robots have a client-server setup where the client dictates what to do and, the server performs the task. In surgical robots, teleoperation is a well-used structure. The surgeon works on the client-side controller and, the server follows those motions on the patient. In this project, my team and I aimed at making a modular teleoperation framework that could help incorporate any client device into any server device. We did have issues automating the inverse kinematics so, we kept the server device constant(ABB IRB 120). We can vary the server device by entering the inverse kinematics for any device.
In the video shown below, we decided to work with a haptic device as the client to get haptic feedback during surgeries. The haptic feedback is hard to show in the video. In the end, there is a separate segment showing the force applied by the motors against the direction of motion. Actuating the haptic device(geomagic touch) is displayed on Rviz. There is a bumper sensor coded at the end of the ABB arm which sends signals back to the Geomagic touch via ROS. The force was applied to the motors.
Software Used: C++, ROS, Gazebo
Manta rays are supremely efficient swimmers and can withstand a wide range of temperatures and pressures. To mimic their body movement would mean to be able to do deep-sea navigation for extended periods. It would also help study manta ray behavior for oceanographers and marine biologists.
In this project, I modeled a manta ray fin from anatomically correct ratios in Solidworks. Then I analyzed this fin in Comsol. I did deflection analysis, stress analysis, flow analysis with a velocity of 5 m/s for water. It helped me understand which parts of the fin endure more stress and need more reinforcement while designing. The video shows the results of this analysis.
Software Used: Solidworks, Comsol
During surgery on organs that move involuntarily, even under anesthesia, the surgeon moves the instruments to compensate for this motion. It means that it is the surgeon's job to synchronize their movements to the patient's. To make their job easier, my team and I worked on a model that would help the surgeon operate as the system takes care of the motion compensation.
We achieved this on a simulation of the Davinci PSM and MTM models on gazebo using ROS. The PSM moved in a combined motion of the MTM and the compensated tissue movement. In the simulation, the platform moves in the form of a randomly generated Fourier transform to simulate tissue. We used an Extended Kalman Filter(EKF) to predict the next position of the platform. The video below shows the results of this model.
Software Used: C++, Gazebo,ROS
There is a boom in interest in self driving cars over the past few years. This project focuses on an algorithm that helps the car stay in lane as well as avoid obstacles safely and return to the lane. This was done using fmincon and yalmip libraries in matlab to optimize the path and produce primitives and reference path lines.
The video below shows the red line (the car) avoiding the blue dot (the obstacle) and rejoining to the keeping the blue stars(the reference trajectory primitives).
Software Used: Matlab
Manta rays can swim very efficiently due to the way they flap their fins. In this project, my team and I wanted to try and replicate this motion using smart materials. We designed a manta ray fin mold in Solidworks and then got the mold 3D printed. We filled the manta ray models with silicone ecoflex-30. Some manta rays had Nitinol wires in them during molding that had been pre-trained to fold in one direction, while others had wires put in them after being molded. Another model was made of a mold with chambers for air to go in.
We then applied electricity to the nitinol wires to compare how pre-trained wires worked against the wires we pushed in after molding. We also tested the pneumatic manta ray to see how it would compare to the electric actuation. The results are in the video below.
Software Used: Solidworks, Ultimaker
Autism Spectrum disorder(ASD) not only affects children's social skills but motor skills as well. For my Bachelor's thesis, I designed, fabricated, and programmed a kiosk to help children better their motor skills. Various factors have influenced the design. Autistic children can be sensitive to different stimuli like touch or visual cues such as the texture of balls or LED lights.
I included different skill exercises like turning, pressing, picking up, placing, throwing, rolling, and depth perception. I integrated sensors like IR, Ultrasound, and limit switches to track progress. DC motors actuate different motions. One PIC board and one Arduino board control these devices. Programming stores and tracks the progress of each child. The image below shows the final setup.
Software Used: Embedded C, Solidworks
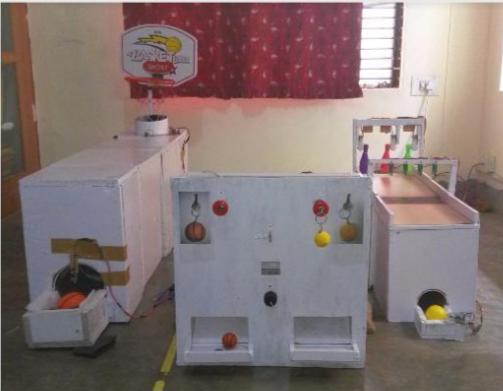
Programming Languages
C++
python
QNX
C#(.NetFramework)
Codesys
Matlab and Simulink
Software and Tools
ROS
Gazebo
Git
LabView
Design Software
Solidworks,ProE, Autocad
Comsol,Ansys
Hardware
Aurduino, PIC boards
IR sensors, Ultrasonic Sensors, limit switches
DC and Servo motors
Moorthy, R., Iyer, K., Krishnan, R., et al. (2019). Enhancement of psychomotor skills in children with autism spectrum disorder by employing a mechatronic training kit. Paladyn, Journal of Behavioral Robotics, 10(1), pp. 1-13. Retrieved 26 Dec. 2018, from doi:10.1515/pjbr-2019-0001
Enhancement of Psychomotor Skills
Raj, Nijin J., Kritika Iyer, and A. K. Dash. "Design, fabrication, kinematic analysis and control of a 3-DOF serial manipulator." Next Generation Intelligent Systems (ICNGIS), International Conference on. IEEE, 2016.
Kinematic analysis of 3DOF Manipulator
Iyer, Kritika, et al. "Application of image processing for a bubble column reactor." Computational Intelligence and Computing Research (ICCIC), 2013 IEEE International Conference on. IEEE, 2013.
Application of Image Processing